Finding the appropriate screw jack depends on several variables, including its load capacity, travel speed, duty cycle and power requirements.
Machine screw jacks offer lower frictional potential when it comes to dynamic loads than ball screws; however, they require more power and may slide backward if your system loses power or the brake motors fail.
1. Load Capacity
Load capacity is one of the key aspects in selecting an ideal screw jack, as it determines if it can support the weight you intend for it to carry and how much force can be controlled through its handle.
In some applications, jacks that can accommodate greater than one ton may be better suited to their task. Their capacity also influences travel speed, efficiency and duty cycle.
Screw jack capacities will depend upon several variables, including ambient temperature, service factors and possible lateral loads or shocks. Therefore, it is crucial that all these aspects are carefully taken into consideration before choosing an ideal screw jack for any given application.

2. Travel Speed
Travel speeds for screw jacks depend on factors like input RPM, load, internal ratio and lead. On average, they range between 375mm per minute for worm gear screw jacks and 500mm per minute for bevel gear jacks.
A worm gear screw jack requires from three to 100 turns on its input shaft per linear inch traveled, depending on input rpm and ratio of gears. This number multiplied by desired travel rate equals torque required at motor.
Travel rate of jacks is often an important consideration when selecting the appropriate size, particularly with longer lift shafts. Critical speed also plays an important role for tension only jacks.
When selecting a screw jack for a particular application, there are several factors to consider. One important consideration is the load capacity required – the screw jack must be able to safely lift and support the weight of the load being lifted.
Another factor to consider is the speed and precision required. A translating screw jack, for example, is ideal for applications that require precise, linear motion. These jacks are designed to convert rotary motion into linear motion, allowing for smooth and accurate movement.
In addition to load capacity and speed/precision requirements, other factors to consider when selecting a screw jack include the environment in which it will be used, the amount of travel required, and the level of control needed over the lifting process.
For example, if the application involves exposure to harsh chemicals or high temperatures, a stainless steel screw jack may be the best choice. If the load must be lifted to a certain height and held in place for an extended period, a self-locking screw jack can provide added stability and safety.
Ultimately, selecting the right screw jack for a given application requires careful consideration of all relevant factors. By taking the time to evaluate the load capacity, speed/precision requirements, environmental conditions, travel distance, and control needs, users can ensure they select the most appropriate screw jack for their specific application.
3. Efficiency
Based on your application, the efficiency of a screw jack can make an immense difference. It may require less energy to operate than hydraulic jacks and could potentially save money over time.
Efficiency can also depend on whether or not a jack is being utilized continuously, for instance an airplane with an aircraft tilt station platform which must be regularly adjusted may need multiple ball screw jacks syncronized with its CAN bus network to ensure effective performance.
Machine screw jacks may be better suited to systems requiring only occasional adjustments, as they tend to be self-locking – meaning they won’t slide backward easily when power is lost and therefore may make for more efficient performance in many applications.
4. Duty Cycle
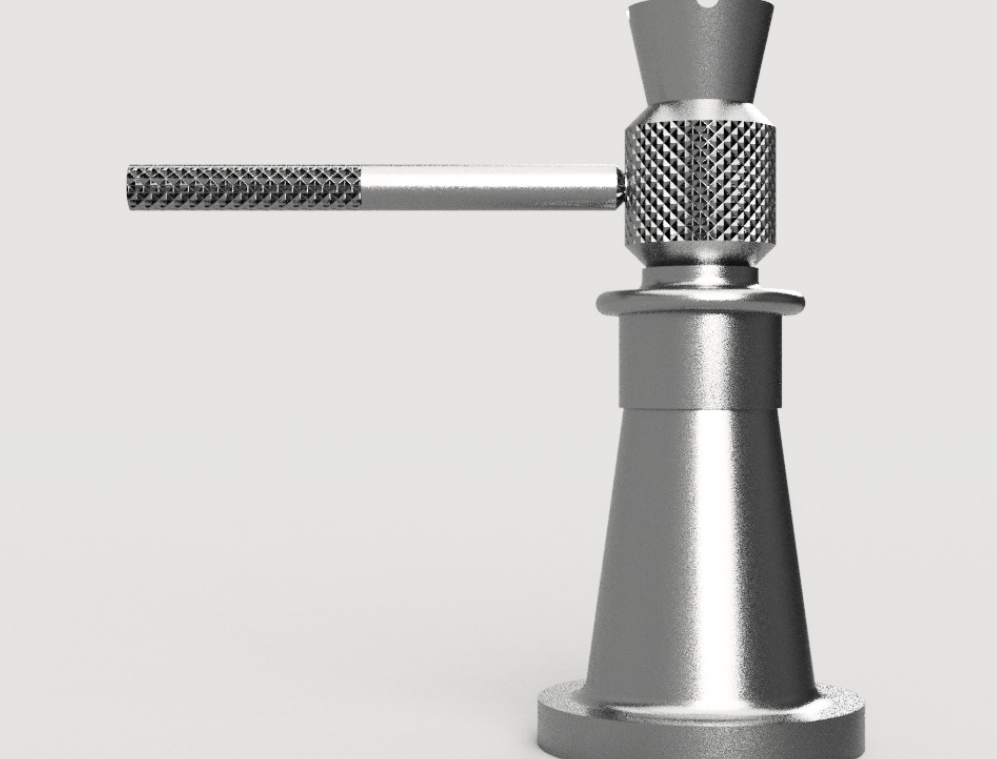
Duty cycles of screw jacks are of primary concern in many applications, as this determines whether a smaller or larger motor should power them.
A higher duty cycle might indicate that lifting, lowering, pushing or pulling can occur more efficiently with reduced energy use and costs, helping the system reach sustainability objectives more easily.
Machine screw jacks may offer greater duty cycles in certain applications due to their increased friction rate which requires approximately twice as much input torque for operation.
5. Power Requirements
A screw jack is a mechanical transmission device used to convert rotational motion to linear movement. It can be used to push, pull, tension, lock/unlock/tilt pivot roll and slide loads of all sizes and types.
Screw jack power requirements depend on its components and their configuration. Each adds drag to the overall system, which may increase motor horsepower requirements by 30% or more.
Before selecting a motor, it is crucial to first determine your total system power requirements and then choose one which can meet them without exceeding thermal limitations.